فصلنامه سیم و کابل
انتخاب مارپیچ و ملاحظات به اکسترودر برای پوشش های سیم و کابل
یک رویکرد برای تمام حالات مناسب نیست، به ویژه زمانی که باید روش بهینه ای برای تنظیم مواد مختلف غیر فلزی در
ساخت کابل استفاده شود.
مقدمه
با توجه به پیشرفت روزافزون صنعت سیم و کابل درتمام دنیا و کاربری انواع آن مطابق با نیازهای مصرف کننده در مکان های
مختلف، پلیمرها نیز نقش پر رنگتری یافته اند. از طرفی سازندگان ماشین آلات نیز به دنبال بهنگام سازی تجهیزات خود به
جهت فرآیند سازی انواع پلیمر با شرایط آسان نموده اند. فرآیند اکستروژن به جهت فرآیند کردن پلیمرهای مختلف و پیوسته
بودن تولید از اهمیت ویژه ای برخوردار بوده است. برای این منظور انتخاب اکسترودر (سیلندر و مارپیچ) به تناسب نوع پلیمر
بسیارحائز اهمیت است.
در اکسترودرهای پوشش دهنده کابل معمولاً پلیمرهای متعددی درکنار شرایط کاری متنوع بکار می رود و یا شرایط کارکرد
متفاوتی در تولید مورد استفاده قرار می گیرند. انتخاب مارپیچ مناسب برای عملکرد بهینه از نیازهای مهم اولیه برای به
حداکثر رساندن کارآیی و سوددهی محسوب می شود . مارپیچ ها درطی سالها تکمیل شده و مارپیچ های مانع هنوز به
طور وسیعی بکار می روند، اما مارپیچ های قدیمی ساده هنوز به خوبی در برخی کاربردها مورد استفاده قرار می گیرند.
این مقاله در خصوص مارپیچ و ویژگی های اکسترودر برای بسیاری از کاربردهای سیم و کابل در دنیای امروزی بحث می کند.
طراحی های مارپیچ با مارپیچ های مترینگ ساده آغاز شد که برخی پلیمرها را به خوبی به عمل آورده ، اما امروز بازدهی آن
برای اکثر پلیمرهای معمول پائین است. (شکل ۱ بالاترین مارپیچ بین سه مارپیچ را نشان می دهد). با گذشت زمان مارپیچ
های مترینگ برای به دست آوردن خروجی بیشتر تغییر یافتند. این کار اساساً به وسیله آزمون وخطا انجام می گرفت، به
طوری که مارپیچ ها با عمق شیار بیشتر و طول قسمتهای متفاوت آزمون و مقایسه می شدند. برخی مواد با قابلیت
پرکنندگی زیاد روی مارپیچ های مترینگ با عمق بیشتر عملکرد بهتری داشته و هنوز از انواع آن با مارپیچ های امروزی
استفاده می شود.
پلی اتیلن نیمه هادی با قابلیت کراس لینک (XLPE) با مارپیچ های مترینگ که قابلیت برش کمی دارند به خوبی عمل می
کند و هنوز به طور معمول از همین نوع مارپیچ استفاده می شود. XLPE غیر هادی و موادی که قابلیت پرکنندگی ندارند در
مارپیچ مترینگ به خوبی عمل نمی آیند و در اینجا نیاز به اضافه کردن کی بخش مخلوط کننده است. (شکل ۱ وسط) این
قسمتهای مخلوط کننده برای اولین بار به صورت ردیفی از پینها که حدود ۵۰ درصد از ناحیه شیاردار را مسدود کرده بودند
ساخته شدند. با بکارگیری طرح مخلوط کننده مادوک ، همه مواد به سمت موانعی فشرده می شوند که در فاصله ای
نزدیک بهم قرار گرفته اند. مخلوط کننده پین دار بر خلاف مخلوط کن مادوک شرایط مناسبی را برای عبورآسان جریان مواد
فراهم نمی کردند. مخلوط کننده مادوک با گذشت زمان بهینه سازی شد و نسبت به تصویر درج شده دچارتغییراتی شده
است از جمله این تغییرات ایجاد شیارهایی درجهت محوری روی آن است.
مخلوط کننده امروزی اغلب دارای تیغه های مارپیچی بوده و شیارهای عمق دار برای بهبود جریان در انتهای شیارها طراحی
شده اند یعنی درست برخلاف شیارهای عمیق قدیمی ساخته می شوند.
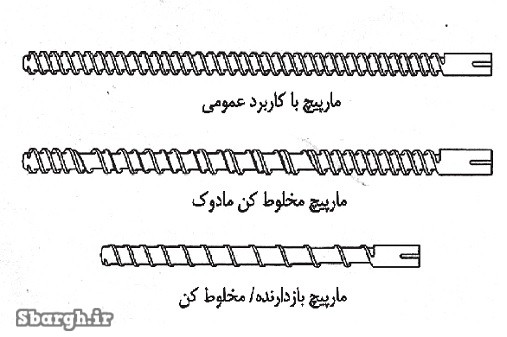
مخلوط کننده هایی با ظاهری که کمترین افت جریان را ایجاد کند برای به عمل آوردن XLPE و پی وی سی و سایر پلیمرهای
فسادپذیر استفاده می شود. تغییرات رنگ به وسیله جریان سیال میان قسمت های مخلوط کننده ایجاد می شود (شکل
۳)
اضافه کردن قسمت های مخلوط کننده به مارپیچ های مترینگ امکان ساخت با شیارهای عمیق تر را فراهم می کند و
بنابراین اجازه عبور مقدار خروجی بیشتری در یک سرعت مشخص به مارپیچ داده می شود. با اضافه شدن مقاومت و تنش
برشی بخش مخلوط کنندگی به مارپیچ، دمای ذوب در مقایسه با مارپیچ های بدون میکسر اضافه خواهد شد. اگر مجاری
مارپیچ را بتوان بدون از دست رفتن کیفیت ذوب عمیق تر ساخت به دلیل ایجاد انرژی اضافی مارپیچ مخلوط کننده قادر خواهد
بود به نسبت خروجی بیشتری دست یابد و در نتیجه خروجی را در دورکمتری ایجاد کند.
سرعت مارپیچ پارامتری است با بیشترین تأثیر روی دمای ذوب، بنابراین مقایسه میزان خروجی در یک دمای ذوب داده شده،
معمولاً انتخاب یک مارپیچ مخلوط کننده را تأئید می کند تا زمانی که مارپیچ اجازه شیارهای عمیق تر و دور کمتری را می
دهد. فرآیندهایی که اجازه عملکرد با سرعت بیشتر مارپیچ را می دهند ( FPVC و پلی اتیلن و غیره) می تواند انتخاب
مناسب و اختصاصی برای مارپیچ های مخلوط کننده باشد. بالا بودن سرعت مارپیچ، به ویژه زمانی که شیارهای مارپیچ برای
به حداکثر رساندن میزان خروجی عمیق تر شده باشند برای نگه داشتن کیفیت ذوب مشکلات زیادی به همراه دارد.
درجایی که مارپیچ های mixing/metering به مرز کارآیی شان می رسند خود را نشان می دهند (شکل ۱ پایین). این طرح
ها ثبات بهتر پمپ کردن و عمق بیشتر شیارها را به ویژه زمانی که با قسمت مخلوط کننده تغذیه می شود فراهم می کند.
در سرعت های زیاد مارپیچ، ثبات عملیات پمپاژ (تغییرات تلرانس محصول) با یک مارپیچ مترینگ معمولاً بدتر شده و طرح
مارپیچ مانع، باعث ذوب مناسب لایه های جامد خرد شده و پمپ کردن یکنواخت می شود. اگر مارپیچ مانع به طور صحیح
برای یک پلیمر و یک شرایط خاص یک فرآیند طراحی شود، لایه های (مواد) جامد می توانند با هم در کی شیار (گام) و مواد
ذوب شده در شیار (گام)خودش به دور از لایه های جامد نگه داشته شوند و به این ترتیب از ایجاد اثرات بی ثباتی روی
مارپیچ مترینگ جلوگیری خواهد شد (شکل ۲). اکثریت مارپیچ های امروزی با خروجی بالا برای کنترل تلرانس تولید مارپیچ
های مانع هستند. مارپیچ های مانع با خروجی زیاد به طور نمونه شامل یک قسمت مخلوط کننده هستند.
فقط برای کاربردهایی که خروجی کمتر مورد نیاز است مارپیچ می تواند بدون اشکال دارای شیارهای سطحی و حذف
قسمت مخلوط کننده باشد. قسمت مانع برای کنترل ثبات پمپ کردن در اکسترودر طراحی شده و قسمت مخلوط کننده
روی ثبات فشار در انتهای سیلندر اکسترودر اثر قابل ملاحظه ای نمی گذارد. طرح های میکسر گوناگونی درطول سالها با
ادعاهای زیاد عرضه شده اما انتخاب مارپیچ مطلوب معمولاً همراه با یک جریان خطی شکل و قسمت مخلوط کننده فشرده
است.
یک مخلوط کننده دو برابر قطر از طول مارپیچ را شامل می شود که معمولاً کافی است. به علاوه باید به گونه ای طراحی
شود که میزان برش کم مورد نیاز برای حصول اطمینان از کیفیت خوب ذوب و مخلوط شدن مورد نیاز به دست آید.احتمالاً
ساده ترین راه برای اداره کردن مورد قابل اجرا، در نظر داشتن پلیمرهای متفاوت است که درکاربرد پوشش دهی کابل ها با
آن مواجه می شویم و به طور خلاصه درباره مارپیچ و نکات برجسته کارآیی اکسترودر همانطور که در ادامه آمده است بحث
می شود.
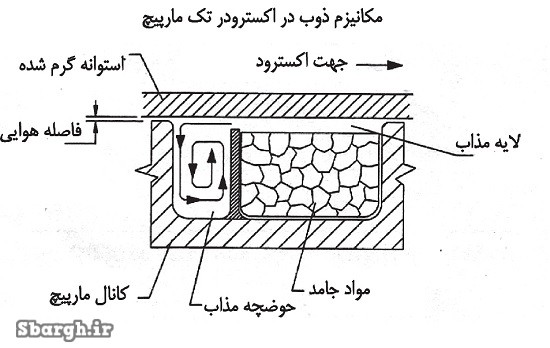
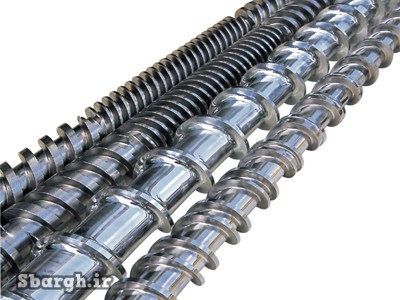
پلی ونیل کلراید (پی وی سی) :
پی وی سی درکاربردهای سیم می تواند طیفی از نرم تا نیمه سخت باشد. هرچه پی وی سی نر متر (با سختی کمتر)
باشد، شیارهای مارپیچ به عمق کمتری نیاز داشته و برش بیشتر یک مخلوط کننده یا قسمت مانع که مطمئناً برای ذوب
کامل مواد خروجی از اکسترودر نیاز است. اساس طرح مارپیچ با مارپیچ های مترینگ که شیارهائی درامتداد سراسر طول
مارپیچ داشته شروع شده است. خنک کننده مارپیچ (چرخش آب درون مارپیچ) بکار رفته به مارپیچ مترینگ اجازه می دهد تا
در سرعت های معمولی ذوب کردن کامل پلیمرها را انجام دهد. بدون خنک کنندگی آب، طرح های مارپیچ مترینگ FPVC
قدیمی پی وی سی را به طور کامل ذوب نخواهد کرد و سطح اکسترود شده موج دار خواهد بود و یا به طور ناچیز مخلوط
می شود. قسمت های مخلوط کننده و طرح های اصلاح شده مارپیچ اجازه حذف آب خنک کننده را داده و در نهایت موجب
میزان خروجی بیشتر می شود.
خنک کننده آب درون مارپیچ باعث افزایش نیازهای تعمیراتی می شود. همچنین توانائی پمپ کردن مارپیچ را به میزان ۵۰
درصد در مقایسه با یک مارپیچ بدون خنک کننده کاهش می دهد.
مارپیچ های خنک کننده با آب برخلاف مارپیچ های مخلوط کننده یا مارپیچ های / barrier mixing این روزها کمتر یافت می
شوند. بیشترین میزان کاربردها را تقریباً همیشه مارپیچ طرح های barrier/ mixing دارد. سیلندرهای اکسترودر با سایز ۵/ ۳
اینچ یا ۵/ ۴ اینچ با هوا خنک می شوند. سایز ۶ اینچ و ماشین های بزر گتر معمولاً با آب خنک می شوند. عمده ماشین
های بزرگ کارایی آب را قابل توجیه می سازند. هر جا که ممکن باشد خنک کننده هوا، با توجه به سادگی و مزایای تعمیر
و نگهداریش استفاده می شود. مارپیچ ها معمولاً از یک نوع فولاد با گرید مناسب (برای مثال AISI 4140) ساخته می
شوند و پره های نوک معمولاً به وسیله جوش خوردن روی یک ماده سازگار انتخاب شده با مواد پوشش داده شده سیلندر
سخت کاری می شوند. سیلندر و مارپیچ اغلب شامل مواد تنگستن کار باید برای فراهم کردن دوام بیشتر با مواد پی وی
سی پر کننده درکاربردهای سیم های پوشش دار هستند.
یک اکسترودر با قطر ۵/ ۴ اینچ با نسبت طول به قطر، (L/D) 24:1 معمولاً یک الکتروموتور ۱۵۰ یا ۲۰۰ اسب بخار ( HP )
خواهد داشت که در ۱۰۰ دور/دقیقه حداکثر سرعت مارپیچ برای بیشترین خروجی پی وی سی تنظیم می شود.

پلی اتیلن :
شامل خانواده بزرگی از محصولات شامل: پلی اتیلن با چگالی کم ، پلی اتیلن با چگالی متوسط، پلی اتیلن با چگالی زیاد ،
پلی اتیلن خطی با چگالی پائین MPE (خانواد های از پلی اتیلن متالوسن) است. این مواد از مارپیچ مترینگ به مارپیچ
مخلوط کننده و در حال حاضر مارپیچ barrier / mixing تغییر یافته اند. مارپیچ مترینگ استفاده شده، ذاتاً خنک کننده با آب
نیست، چون کارآیی آن مثل مارپیچ خنک شونده پی وی سی نیست.
مارپیچ مناسب در طی سالهای متمادی یک مارپیچ / metering meter بود، اما در بیشتر موارد نتایج بهتری به وسیله مارپیچ
های mixing /barrier امروزی به دست آمد. (زمانی که به درستی طراحی شده باشند). مواد پلی اتیلن با چگالی بیشتر
(چگالی متوسط ، چگالی زیاد ، چگالی خطی کم و بسیاری MPE ها یک طرح مارپیچ با برش کمتر (شیارهای عمیقتر) را
بکار می برند، مهم نیست که طرح اصلی کدام است. اگر یک اکسترودر ۵/ ۴ اینچ و نسبت طول به قطر ۲۴:۱ (L/D) باشد،
برای به عمل آوردن پلی اتیلن با چگالی کم ممکن است با یک موتور ۱۵۰ اسب بخار ( HP ) که در ۱۰۰ دور/ دقیقه RPM کار
کند. حداکثر سرعت مارپیچ کارآیی داشته باشد، در حالی که پلی اتیلن ها با ویسکوزیته بالاتر به یک موتور ۲۰۰ یا حتی ۲۵۰
اسب بخار ( HP ) در ۱۰۰ دور/دقیقه RPM نیازخواهند داشت. اکسترودر پی وی سی، تا ۵/ ۴ اینچ با هوا خنک خواهد شد و
معمولاً از ۶ اینچ و بیشتر با آب خنک می شود.
مارپیچ از یک نوع فولاد مناسب است که از جوش خوردن مواد به پره های نوک برای مقاومت در برابر سایش ساخته می
شود. پلی اتیلن با چگالی زیاد ماده ای است که از مواد مقاوم در برابر سایش جوش خورده مختلف که امروزه در دسترس
است به دست می آید. تزریق پلی اتیلن خطی با چگالی کم و پلی اتیلن با چگالی متوسط مشابه با تزریق پلی اتیلن
چگالی زیاد است و شرح فرآیند مشابه دارند. خانواده PEM شامل یک دسته از گرانروی متفاوت برای انتخاب طرح در مارپیچ
است. بعضی از گشتاور بیشتری استفاده می کنند و عدم ثبات ذوب از خرد شدن زود هنگام لایه های جامد درطول مارپیچ
ارائه می دهند. این انتخاب های MPE به مارپیچ مانع نیاز دارد. قسمت مانع می تواند بی ثباتی زود هنگام ذوب را تعدیل
کند.
پلی پروپیلن :
میزان خروجی پلی پروپیلن به اندازه پلی اتیلن بازدهی ندارد. با در نظر گرفتن یک مارپیچ مشابه هر دو کمیت، تغذیه شده و
ذوب یافته و نتیجه این می شود که مقدار خروجی برای پلی پروپیلن به میزان ۴۰ درصد کمتر از پلی اتیلن باشد.
هوموپلیمرها کار آیی کمتری در مقابل کوپلیمرها دارند، اما هر دو نوع پلی پروپیلن به طور قابل ملاحظه ای در اکسترود
شدن در مقایسه با پلی اتیلن بازدهی کمتر دارند.
اکسترودرها برای اکسترود کردن پلی پروپیلن اغلب بلندتر از ۲۴:۱ هستند، چون مقدار خروجی تقریباً به طور خطی با طول
سیلندر افزایش می یابد. یک اکسترودر ۳۰:۱ بیش از ۲۵-۲۰ درصد مقدار خروجی بیشتر درمقابل یک اکسترودر ۲۴:۱ دارد.
یک اکسترودر ۳۴:۱ حتی خروجی بیشتری نیز ارایه می کند. طرح مارپیچ بهینه یک مارپیچ mixing/barrier خواهد بود که در
نواحی شروع و کانال های ذوب تغییر ماهیت بدهد تا بتواند پلی اتیلن و پی وی سی را فرآیند کند. زمانی که کاربرد پلی
اتیلن مدنظر باشد، اولین مارپیچ منتخب مارپیچ های مترینگ و سپس مارپیچ های مخلوط کننده است.
نایلون :
متداولترین مواد نایلون، نایلون ۶ و نایلون ۶/ ۶ هستند. برای حداکثر مقدار خروجی روی اکسترودر تعیین شده، هر دو روی
مارپیچ / barrier mixing بهترین فرایند اکسترود شدن را دارند. مقادیر کمترخروجی در یک مارپیچ مترینگ یا مارپیچ مانع بدون
قسمت مخلوط کننده به دست می آید. تفاوت بسیار کمی در عملکرد اکسترود شدن بین انتخاب این نایلون های متداول
وجود دارد، اما یک مارپیچ می تواند صرفنظر از نوع، آن برای تغذیه کردن هر دو طراحی شود. اکسترودرهای نایلون معمولاً با
هوا خنک می شوند، حتی در اکسترودرهای بزرگتر با توجه به وجود دمای زیاد همین روش بکار می رود . متالورژی روی
مارپیچ و سیلندر مشابه پی وی سی یا پلی اتیلن است. به دلیل بالا بودن نقطه ذوب نایلون کلمپ های گرم شده یا گرم
کننده فلنج در انتهای اکسترودر نقش مهمی دارد، ساخت مارپیچ با یک سوراخ کوتاه میانی دور از ذهن نیست (بین سه گام
اول) این طرح در زمان چسبیدن نایلون به مارپیچ که حین بروز مشکل در سیستم خنک کنندگی رخ می دهد بکار می آید.
بخصوص زمانی که حین تولید کابل اکسترودر دچار توقف شده یا فرایند تولید به کلی متوقف گردد. خنک کردن تعداد کمی از
اولین پره های مارپیچ (گام های مارپیچ در قسمت تغذیه) در مقدارخروجی تأثیر نخواهد گذاشت، (همان طور که در مارپیچی
که کاملاً خنک کاری شده مشاهده میشو)، اما می تواند از ذوب شدن نابهنگام نایلون که می تواند منجر به چسبندگی به
بدنه مارپیچ و موجب کاهش میزان خروجی و یا توقف کامل شود جلوگیری کند.
فلوئور پلیمرها :
این خانواده از مواد، به دمای زیاد نیاز دارند و در ساخت مارپیچ و سیلندر مربوط باید متالورژی مقاومت در برابر خوردگی مدنظر
قرار گیرد. به طور معمول جنس مارپیچ ها Hastelloy یا Inconel هستند که نیکل زیادی دارند و برای داشتن مقاومت بهتر
فلوئورینها در طول اکسترود کردن بهینه سازی شده اند. ساختار قالب و سیلندر نیز باید شامل نیکل زیادی باشد.
خنککنندگی با هوا در دماهای مورد نیاز در طول سیلندر روشی معمول است و گرم کنها معمولاً بایستی به صورت متناوب
قرار گیرند. اکسترودرهای معمولی دارای گرمکنهای آلومینیومی ریخته گری شده هستند که تا نقطه معین مورد نیاز برای
فلوئورپلیمرها پایداری ندارند. هیترهای ریخته گری برنزی یا هیترهای سرامیکی نواری در اکسترود کردن فلوئوپلیمرها می
توانند بکار روند. طرح مارپیچ با هر دو مارپیچ های مترینگ یا مارپیچ های meter/mixing مقدار خروجی مورد نیاز در یک
اکسترودر مشخص معمولاً، با توجه به محدودیتهای خروجی نامنظم مواد ذوب در خروجی قالب نسبتاً کم است. در میزان
خروجی کم و سرعت پائین مارپیچ، عملکرد مارپیچ مترینگ توأم با کاهش پایداری پمپ است. مارپیچ های فلوئورپلیمرها
محکم نیستند و ظرفیت تحمل گشتاور آنها نیازمند بازبینی است که عملکرد خطر شکستن مارپیچ به حداقل رسانده شود.
لاستیک :
لاستیک شامل اتیلن پروپیلن رابر EPDM ، لاستیک طبیعی و بسیاری از آمیزه هاست. این مواد می توانند گلوله ای شکل
باشند، اما معمولاً نواری شکل هستند. برای استفاده از مواد نواری شکل معمولاً به یک قسمت تغذیه مخصوص در
اکسترودر با یک غلتک قوی برای کمک کردن به نوارها در پره های تغذیه مارپیچ، که معمولاً دارای طول بلند یا پره های دوبل
هستند نیاز است. مارپیچ های مترینگ دارای پره های دوبل با شیارهای عمیقتر هستند یا مارپیچ های مانع عمیق که شامل
مخلوط کننده نیستند. (شکل ۴، اولی و دومی). قسمت مانع، عمل تفکیک ذرات جامد / ذوب شده را مثل فرآیند اکسترود
شدن پلاستیکها انجام نمی دهد، چون لاستیک واقعاً ذوب نمی شود. لاستیک با گرما و انرژی برشی نرم شده و قسمت
مانع در فرآیند مواد کمک میکند که لاستیک در یک دمای ثابت و معین باقی بماند (عملکرد شبیه یک ناحیه مخلوط کننده
طولانی به تدریج). مارپیچ مانع، همچنین به از بین بردن هرگونه بی ثباتی در تغذیه کمک می کند و ثبات پمپ کردن را همان
طور که در فرایند اکسترود کردن مواد پلاستیکی انجام میدهد بهبود می بخشد. لاستیک گلوله ای شکل شده ضرورتاً به
نیروی هدایت کننده تغذیه نیاز ندارد اما از گونه های با عمق یکسان سود می برد، طرحهای مارپیچ با برش کم همانند
مباحث در قسمت تغدیه است.
مواد لاستیکی اغلب قابلیت پرکنندگی زیادی دارند و پره های قسمت نوک مارپیچ آنها باید سطحی سخت داشته باشند.
این سختی می تواند با تنگستن کار باید به وجود آید. بیشتر اکسترودرهای لاستیکی با آب خنک کاری میشوند، چون دمای
سیلندر بسیار پائین بوده ( ۱۵۰ تا ۲۰۰ درجه فارنهایت)، و بازدهی خنک کنندگی با هوا کم است. لاستیک معمولاً چگالی
زیادی دارد. بنابراین گشتاور بالاتر اکسترودر مورد نیاز است، برای مثال یک اکسترودر ۵/ ۴ اینچ با یک موتور ۱۵۰ hp (اسب
بخار) در ۵۰ – ۴۵ دور/دقیقه حداکثر rpm مارپیچ تنظیم شده است. چون لاستیک واقعاً ذوب نمی شود و طبیعت چگالی
بالای آن موجب بالارفتن بیشتر انرژی در طول ماشین می شود، بیشتر ماشین های لاستیکی دارای طول سیلندر کوتاهی
در مقایسه با اکسترودرهای پلاستیک هستند. یک نمونه ماشین لاستیکی دارای نسبت طول به قطر L/D) 15:1) یا ۲۰:۱
است درحالی که اکسترودرهای پلاستیکی ۲۴:۱ و گاهی اوقات ۳۰:۱ هستند. مارپیچ کاملاً هسته دار بوده و آب داغ یا
روغن گرم برای کنترل دمای مارپیچ مورد استفاده قرار میگیرد.
در اکسترود کردن مواد لاستیکی کنترل دمای مارپیچ پیشنهادی یک پارامتر برای کمک به کنترل کیفیت اکسترود شده و
ذخیره دما است. سیلیکون از خانواده لاستیک است و نیاز به دمای کمتر دارد (تنظیمات سیلندر از ۵۰ تا ۶۰ درجه فارنهایت)
آب مارپیچ استفاده شده در دمایی مشابه برای تنظیمات اشاره شده سیلندر تنظیم میگردد. انتخاب مارپیچ به طور معمول
طرحهای مترینگ است و، یا مشابه مارپیچ های مواد لاستیکی با پره های دوبل یا مارپیچ های تک پره با کاهش پوشش پره
جاییکه فشار قالب بالاتر مورد نیاز باشد (شکل ۱ اولی و سومی) طول اکسترودرهای سیلیکون همانند اکسترودرلاستیک
کوتاه هستند، با L/D درحدود ۱۲:۱ – ۸ است. سیلیکون معمولاً دارای تغذیه نواری شکل بوده، بنابراین رو ل های قوی تغذیه
استاندارد هستند. ماشین های قدیمی تر دارای مجرای تغذیه مماسی و بدون غلطک هستند اما وجود غلتکها باعث بهبود
کنترل تغذیه و پایداری کنترل پمپاژ می شود.
پلی اوره تان :
پلی اوره تان ها دارای محدود های از سختی هستند که روی مقدار تنش برشی ایجاد شده در مارپیچ شدیداً اثر می
گذارند. برای دستیابی به یک سطح صاف و ذوب کامل در اکسترودر باید حتما به مقدار تنش برشی دقت شود. بعضی اوره
تان ها ترکیبی از مواد با سختی متفاوت هستند که برای حاصل شدن یک سختی نهایی کار مارپیچ را سخت میکند، چون
باید دو جزء را با چگالی متفاوت ذوب و مخلوط کند. اغلب به دست آوردن ثبات پمپ کردن خوب با اوره تان دشوار است.
نداشتن نتیجه مطلوب ناشی از ذوب زود هنگام مربوط به لایه های جامد در بسیاری از اوره تان ها متداول است و بهترین
راه برای رسیدن به ثبات پمپ کردن خوب با طراحی مناسب یک مارپیچ مانع، محقق میشود. مارپیچ های مترینگ به
قسمتهای مترینگ بلند نیاز دارند. این امر بهترین امکان را برای ثبات پمپ کردن خوب به وسیله از بین بردن بعضی از تغ
ییرهای فشار زود هنگام ایجاد خواهد کرد، اگر چه این مشکل اساسی عدم ثبات را که در یک مارپیچ مانع فراهم میشود را
از بین نمی برد. اوره تان ها به گشتاور متوسط تا زیاد نیاز دارند، چیزی شبیه به پلی اتیلن چگالی زیاد یا پلی اتیلن خطی
چگالی کم.
الاستومرهای ترموپلاستیک :
اگر این مواد بر پایه پلی پروپیلن باشند، طرح مارپیچ همانند نکاتی است که در مورد پلی پروپیلن ذکر گردید. زمانی که
الاستومرهای ترموپلاستیک بر پایه پلی اتیلن بوده بیشتر مواردی شبیه مواد پلی اتیلن باید مدنظر قرار گیرند. این گروه
خانواده بزرگی از مواد با ویسکوزیته های گوناگون هستند و بنابراین سطوح برشی لازم مارپیچ برای کنترل هر نوع از
الاستومرهای ترموپلاستیک تغییر خواهد کرد.
آمیزه های بازدارنده شعله :
نیاز به افزودنی ها برای بازدارندگی شعله و پرکننده ها معمولاً باعث دقت در طرح مارپیچ و سخت کاری کردن سطح
مارپیچ/سیلندر است. معمولاً مارپیچها به برش کمتر طرحهای barrier/mixing نیاز دارند . مارپیچ های قدیمی تر مترینگ
عمیق یا طرحهای meter/mixer به طور منظم در سرعتهای کم کار میکند، که با توجه به حساسیت این مواد به گرما اغلب
تنها محدوده دور/دقیقه برای این است. زمانی که بسیاری از مواد بازدارنده شعله به ۴۰۰ F یا بیشتر می رسند، یک واکنش
دمائی موجب پخش گازهای فرار شده و حبابهایی در محصول نهایی مشاهده می شوند. مشابه مواد با ویسکوزیته بالا،
کمترین برش ممکن اجازه کیفیت ذوب را می دهد و این بهترین طراحی مارپیچ است.یک نمونه مناسب با توجه به قدرت
سایش پرکننده های ارائه شده استفاده از مارپیچ و سیلندرهای سخت کاری شده با مواد تنگستن کارباید است.
پلی اتیلن با قابلیت کراسلینک (XLPE) :
این خانواده از مواد نیز، به ملاحظاتی جهت انتخاب مارپیچ متفاوت نیاز دارند. مواد XLPE نیمه هادی معمولاً روی مارپیچهای
مترینگ یا مارپیچ های meter/mixing فرآیند می شود، که کار کیفیت ذوب و ثبات پمپ کردن را به طور منظم انجام میدهد.
افزودنی های دوده که در مواد نیمه هادی استفاده می شود حین عبور مواد از اکسترودر به وسیله بهبود فرایند انتقال گرما
به درون پلیمرها به فرایند ذوب کمک میکند. ذوب شدن به طور پایدار درست برخلاف پلی اتیلن خالص و به طور وسیع رخ
میدهد. مواد XLPE نیمه هادی معمولاً روی ماشینهای با سیلندر کوتاه اکسترود میشوند، معمولاً ۲۰:۱ و گاهی اوقات حتی
۱۵:۱ (L/D).
مواد XLPE غیرهادی روی مارپیچ های barrier/mixing از طرح برش متوسط یا کمتر، معمولاً روی طول سیلندر با ۲۴:۱ L/D
بهتر کار میکنند. این شامل مواد کراسلینک کننده با پایه سیلان است. مواد سخت شده معمولاً روی لایه های بیرون پره ها
جوش می خورد، و اکسترودر برای اکسترود کردن پلی اتیلن با چگالی بالا یا پلی اتیلن خطی با چگالی کم این گونه ساخته
می شود.
انتظار کلی برای اکسترودرهای پوشش دهنده سیم، تمایل برای فرآیند کردن چندین پلیمر در یک مارپیچ است. این کار
میتواند به خوبی با مارپیچ های مانع امروزی انجام شود، اما به دلیل گسترش پلیمرهای استفاده شده هنوز محدودیت
هایی وجود دارد. طرحهای مارپیچ مترینگ همچنین می تواند چندین پلیمر را روی یک طرح به انجام برساند، اما نتیجه حاصله
در عمل معمولاً بازدهی کمتری از مارپیچ مانع دارند. هنگا تصمیم گیری روی بهترین طرح مارپیچ انتخاب پلیمر برای فرآیند
شدن، مقدار خروجی مورد نیاز، ثبات پمپ کردن مطلوب و فشارهای پیش بینی شده در انتهای مارپیچ باید درتصمیم گیری
ها در نظرگرفته شود.
نتایج :
زمانی که یک انتخاب درست برای همه کاربردها وجود ندارد، تجربه گذشته فرآیند پلیمر داده شده موجب طراحی مارپیچ
هایی می شود که خروجی داده شده و نیاز به ثبات پمپ کردن راکنترل میکند. هنگامی که پلیمرهای متعدد به فرآیند شدن
در یک مارپیچ نیاز دارند باید مشخص شود که کدام نیازها بایستی نادیده گرفته شود تا بهترین طراحی مارپیچ انتخاب شود.
هنگام تصمیم گیری روی بهترین طرح مارپیچ پلیمر فرآیند شونده مقدار خروجی مورد نیاز، ثبات پمپ کردن و فشارهای مورد
انتظار در انتهای مارپیچ باید درتصمیمات مورد توجه قرار گیرد.
ادوارد استیوارد – Edward Steward
مترجم: محمدرضا رئیسی
نشریه داخلی صنعت سیم و کابل – شماره چهل و دوم